A: It depends.If we have bulk goods in stock, we can ship goods within 3 days after the QC process. If we don’t have stock, normally it takes 7-15 days for OEM samples and 20-30 days for bulk goods. If it refers to opening the new mold, it takes an extra 7-15 days to make the mold.
Hex Nuts
Hex Nuts
Standard Spec :ASTM A194,DIN934,DIN439,DIN6330,DIN6915,GB6172,GB6173
Diameter :M4-M72(8#-4”)
Material:Carbon Steel ,Alloy Steel ,Stainless Steel
Class:4.8,5.8,6.8,8.8,10.9,G2,G5
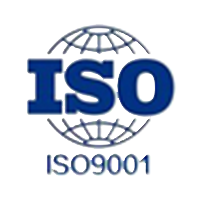
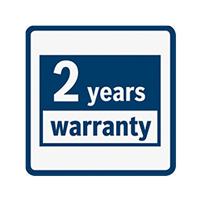
Quote Now
Hex Nuts: Overview
Material:
- Common materials: Carbon steel (Grade 4/8/10), stainless steel (304/316), alloy steel (heat-treated for high strength), brass, or nylon.
- Surface treatments: Zinc plating, hot-dip galvanizing, Dacromet coating, or passivation (stainless steel) for corrosion resistance.
Manufacturing Process:
- Cold Forging: Shapes the hexagonal blank from steel wire, ensuring dimensional consistency.
- Threading: Internal threads are cut via tapping or formed by thread rolling for precision.
- Heat Treatment: Quenching and tempering (for high-grade steel nuts) to enhance hardness and tensile strength.
- Surface Finishing: Electroplating, galvanizing, or coating to improve durability and corrosion resistance.
Key Production Considerations:
- Thread accuracy: Must comply with ISO/DIN standards to ensure compatibility with bolts.
- Hexagon symmetry: Uniform flat-to-flat dimensions for proper wrench engagement.
- Coating uniformity: Prevents thread clogging and ensures smooth installation.
- Deburring: Eliminates sharp edges to avoid thread damage during assembly.
Applications:
- Industrial machinery: Secures bolts in engines, conveyors, and presses.
- Construction: Used in steel frameworks, bridges, and scaffolding.
- Automotive: Fastens chassis, suspension, and engine components.
- HVAC/piping: Joins flanges and pipe fittings with lock nuts (e.g., nylon insert) for vibration resistance.
- Consumer goods: Assembly of furniture, bicycles, and electronics.
Installation:
- Tool selection: Use a wrench or socket matching the nut’s hex size (e.g., 10mm, ½”).
- Alignment: Ensure threads are clean and undamaged; hand-tighten before applying torque.
- Torque control: Follow manufacturer specifications to avoid under/over-tightening (use a torque wrench for critical joints).
- Locking mechanisms: Pair with lock washers, thread-locking adhesives, or nylon-insert nuts in high-vibration environments.
- Inspection: Check for proper seating and thread engagement post-installation.
Note:
Frequently Asked Questions
Get Quote Now!
Welcome to discuss your purchasing requirements with our customer service.